Rapid Ethanol Chilling Freezers

Cryometrix L-80
Max Chiller
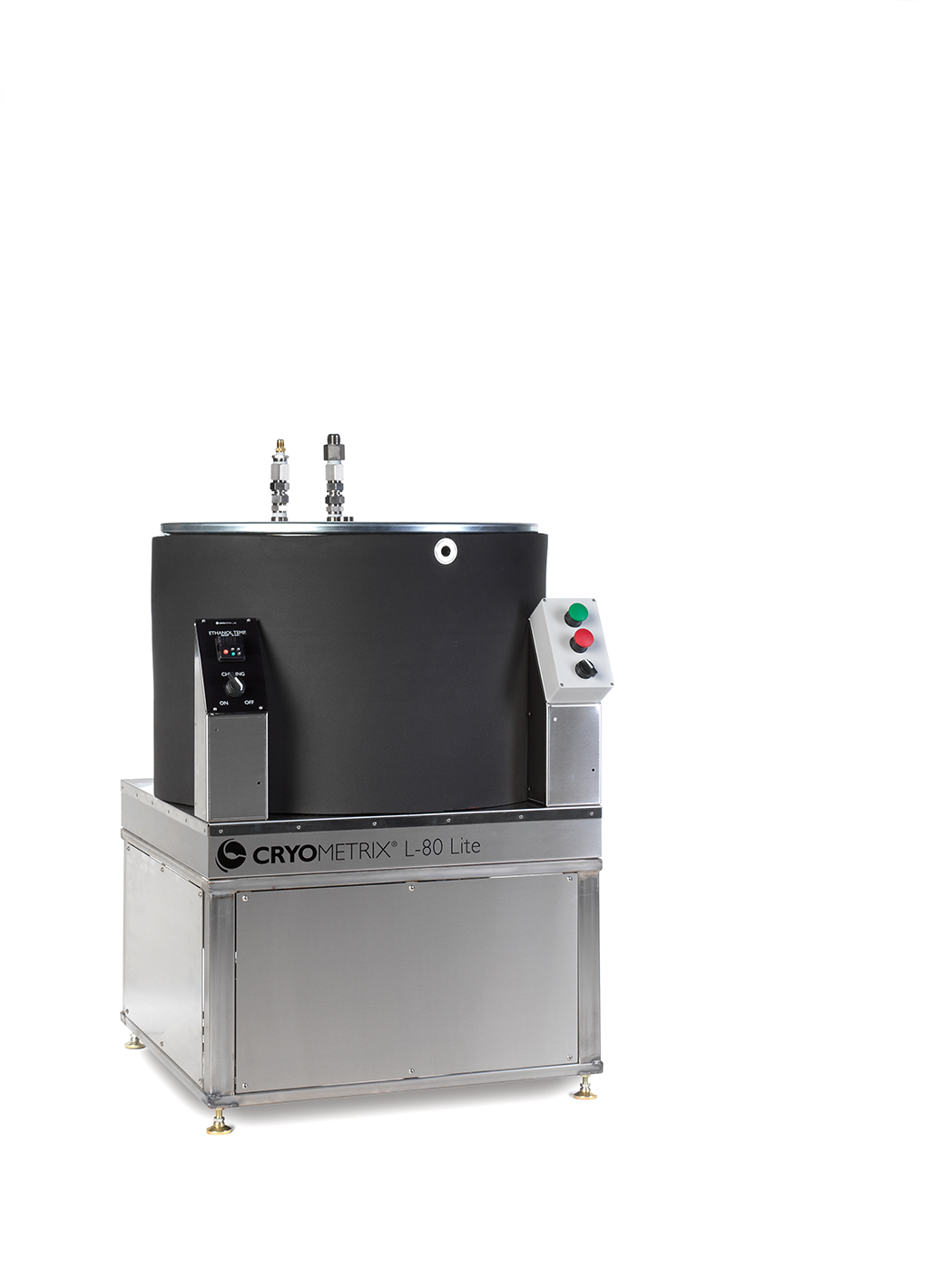
Cryomterix L-80
Lite Chiller
Cryometrix offers innovative rapid ethanol chilling freezers designed to meet the growing demands of the extraction and winterization industries. These advanced machines leverage cutting-edge liquid nitrogen (LN2) technology to provide the fastest chilling times available, significantly enhancing both productivity and energy efficiency. Whether for large-scale CBD extraction or smaller operations requiring fast turnaround times, Cryometrix’s ethanol chillers, including the L-80 MAX and L-80 LITE, deliver industry-leading performance with environmental sustainability at the core.
The Importance of Rapid Ethanol Chilling
In industries like CBD extraction, ethanol is often used as a solvent due to its ability to efficiently extract cannabinoids from plant material. However, the temperature of the ethanol plays a crucial role in ensuring the quality of the extraction process. The warmer the ethanol, the more unwanted plant materials, such as chlorophyll, are extracted, which can lead to impurities in the final product. By rapidly chilling ethanol to subzero temperatures, extraction processes can minimize these unwanted materials, resulting in a purer and higher-quality end product.
Cryometrix’s ethanol chilling freezers, including the L-80 MAX and L-80 LITE, offer solutions specifically designed to meet these needs, ensuring that ethanol is chilled to precise temperatures in record time, all while reducing energy consumption and minimizing the environmental impact.
L-80 MAX Chiller: Maximum Performance for Large-Scale Operations
For industrial-scale operations requiring fast, high-capacity ethanol chilling, the L-80 MAX Chiller is the ultimate solution. This chiller is designed to handle up to 120 gallons of ethanol, making it an ideal choice for companies with significant throughput requirements.
- Unparalleled Speed: The L-80 MAX can chill 120 gallons of ethanol to -40°C in just 25 minutes and to -80°C in 50 minutes, offering one of the fastest chilling processes available in the industry. For smaller batches, it can chill 30 gallons of ethanol to -40°C in as little as 9 minutes, making it a versatile tool for any scale of operation.
- Energy Efficiency: Traditional compressor-based chilling systems are known for their high energy consumption and maintenance needs. The L-80 MAX eliminates these issues by using liquid nitrogen technology, which requires no mechanical compressors. This drastically reduces energy usage by up to 95% compared to compressor-based systems. With no mechanical components to service or replace, this system also reduces maintenance costs, making it a highly cost-effective solution over time.
- Environmental Sustainability: With no exhaust heat and no need for HVAC systems, the L-80 MAX creates a safer and more sustainable working environment. Nitrogen, a natural and abundant element, is used as the cooling agent, ensuring that the system emits only clean nitrogen into the atmosphere, which makes up over 75% of the air we breathe. Unlike traditional refrigerants, which can be harmful to the environment, LN2 is completely eco-friendly.
- Compact Design: Despite its large chilling capacity, the L-80 MAX has a small footprint of just 33” x 33”, making it easy to integrate into even the most space-constrained facilities. The chiller can be placed side by side with additional units, allowing for easy expansion as your business grows.
- Automation and Ease of Use: Designed with the user in mind, the L-80 MAX features a simple one-button operation that allows for automatic fill, chill, and drain functions. With temperature uniformity of ±1°C and built-in data logging capabilities, the system ensures consistent performance while maintaining precise control over the chilling process.
L-80 LITE Chiller: High Performance for Small to Mid-Sized Operations
For companies with smaller chilling needs or limited space, the L-80 LITE Chiller offers a more compact and affordable solution without sacrificing performance. Designed to be the “younger brother” to the L-80 MAX, the L-80 LITE is optimized for operations that require rapid chilling of smaller quantities of ethanol.
- Fast and Efficient: The L-80 LITE can chill 30 gallons of ethanol to -40°C in just 8 minutes and to -80°C in 19 minutes. This makes it an excellent choice for businesses needing fast turnaround times, such as smaller CBD extraction facilities or research labs.
- Modular Design for Scalability: One of the standout features of the L-80 LITE is its modular design, which allows users to upgrade the system as their needs grow. This flexibility makes the L-80 LITE an ideal choice for growing businesses that want to start with a smaller system and scale up over time.
- Low Energy Consumption: Like its larger counterpart, the L-80 LITE uses liquid nitrogen technology, which requires no mechanical compressors. This not only cuts down on energy usage but also eliminates the need for expensive HVAC systems, significantly reducing operational costs.
- Portable and Space-Efficient: With a small footprint of just 33” x 33”, the L-80 LITE is portable and can fit easily into almost any workspace. Its compact size and ability to be placed side by side with other units make it a perfect solution for smaller facilities with limited floor space.
- Safety and Compliance: The L-80 LITE is designed for Class I, Division 2 environments, making it suitable for use in facilities handling flammable solvents. The system’s closed nitrogen system ensures that no liquid nitrogen comes into contact with the operator or the product, further enhancing safety.
Applications of Cryometrix Ethanol Chillers
Cryometrix ethanol chillers are highly versatile and are used in a variety of industries, including:
- CBD Extraction: One of the primary applications of Cryometrix chillers is in CBD extraction, where ethanol is used to extract cannabinoids from hemp or cannabis plants. Rapid chilling improves the quality of the extraction by reducing the amount of unwanted plant materials that are extracted along with the cannabinoids.
- Winterization: After extraction, ethanol chilling is also essential in the winterization process, which removes plant fats, waxes, and other impurities from the crude extract. The ultra-low temperatures provided by Cryometrix chillers ensure that these unwanted materials are efficiently removed, resulting in a cleaner and higher-quality end product.
- Research and Development: The compact size and affordability of the L-80 LITE make it an excellent choice for research labs and R&D facilities that require rapid chilling of smaller quantities of liquid for various experiments.
- Industrial Manufacturing: For large-scale production facilities, the L-80 MAX offers a powerful solution for chilling liquids used in manufacturing processes, enabling faster production times and greater throughput.
Environmental and Economic Benefits
Cryometrix’s ethanol chillers are designed with both environmental sustainability and cost-efficiency in mind. The use of liquid nitrogen as a cooling agent means that no harmful refrigerants like CFCs or HCFCs are used, reducing the environmental impact of the system. Additionally, the elimination of mechanical compressors and HVAC systems leads to significantly lower energy usage and maintenance costs, providing long-term savings for businesses.
Why Cryometrix Ethanol Chillers Are the Ultimate Solution for Your Extraction Needs
Cryometrix’s rapid ethanol chilling freezers, including the L-80 MAX and L-80 LITE, are revolutionizing the extraction and winterization industries. With unmatched speed, energy efficiency, and environmental sustainability, these chillers are the ideal choice for businesses looking to enhance their production processes. Whether you need to chill 120 gallons of ethanol for industrial-scale CBD extraction or 30 gallons for a smaller operation, Cryometrix has the perfect solution to meet your needs.